Обработка металлов резанием: механическая. Механическая обработка металла: виды и способы
ГК «НЗМК» производит металлические изделия, продукцию из металла, и оказывает такую услугу, как механообработка деталей из металла .
Услуги по механической обработке металла. Возможности завода
Механическая обработка не оказывает прямого или опосредованного влияния на изменение внутренней структуры материала, обеспечивая только изменение его конфигурации и геометрических размеров.
Клиенты имеют возможность разместить у нас заказы на выполнение обработки посредством:
- Резания заготовки;
- Пластического деформирования:
- o Ковка;
- o Штамповка;
- o Прессование;
- o Накатка резьб;
- Деформическим резанием;
- Электрофизической обработкой:
- o Электроэрозионная;
- o Электрохимическая;
- o Электрическая сварка (дуговая);
- Проведения электрообработки.
Механическая обработка металла резанием востребована наиболее часто. На Новомосковском заводе металлоконструкций резание выполняется следующими видами:
- Точение - производится в тех случаях, когда заготовка почти совпадает по размерам с нужной деталью. Необходимая заказчику механообработка металла выполняется на станках различного назначения:
- o Токарных;
- o Протяжных и фрезерных;
- o Сверлильно-расточных и т.п.
- Сверление;
- Долбление;
- Протягивание;
- Фрезерование - осуществляется на специальных станках;
- Строгание - выполняется на станках и поперечном оборудовании строгальном;
- Шлифование - выполняется на шлифстанках
Услуги по механической обработке металла предоставляются с использованием ряда вспомогательных видов упомянутой обработки.
Этапы механообработки деталей из металла по чертежам заказчика
Получив от заказчика комплект рабочей документации, технологи ГК «НЗМК» определяют:
- возможно ли изготовление деталей, соответствующих ТЗ, на имеющемся оборудовании;
- какие станки для этого потребуются;
- на каких режимах должна вестись обработка и т.п.
достаточно часто после этого принимается решение об обработке заготовки резанием. В процессе выполнения данной операции снимается избыточный слой металла (припуск). После этого деталь соответствует габаритам, заданным чертежом заказчика.
Решение обточить заготовку принимается в тех случаях, когда она по своим геометрическим характеристикам незначительно отличается от тех, что должна иметь готовая деталь.
Механическая обработка сверлением позволяет выполнить необходимые отверстия в конструкции. А долбление или фрезерование - придать изделию требуемые геометрические параметры.
В отдельных случаях, заготовки обрабатываются давлением. Например, механическая обработка металлов (цветных) часто предусматривает использование горячей кузнечной обработки. При этом ковка может выполняться одним из следующих вариантов:
- свободная;
- с использованием штампа кузнечного.
Альтернативным вариантом обработки может выступать технология прессования. На Новомосковском заводе металлоконструкций имеется несколько прессов различной мощности и назначения.
В машиностроительной, металлообрабатывающей отраслях, в строительстве используют различные способы обработки металла, резание – один из их разновидностей.

Поскольку металлических деталей существует огромное множество, они различаются по форме, размеру, весу, составу сплава, поэтому и обработка металлов резанием также осуществляется несколькими способами. Можно выделить основные:
- точение;
- сверление;
- фрезерование;
- строгание;
- шлифование.
Каждый вид предполагает использование специализированного оборудования – часто это стационарные станки.
Точение металлических деталей
Этот способ применяется, когда исходную заготовку необходимо в незначительной мере доводить до нужных размеров и конфигурации. Для этого специалисты используют токарный станок, комплект сверл или резцов. Деталь, которую нужно обработать, помещают в специальное вращательное устройство, вокруг которого движется режущий механизм.

Благодаря оказываемому усилию кромка острия сверла врезается в деталь и удаляет лишний слой, который превращается в разного рода стружку. В зависимости от того какого вида выполняется резка стружка может быть:
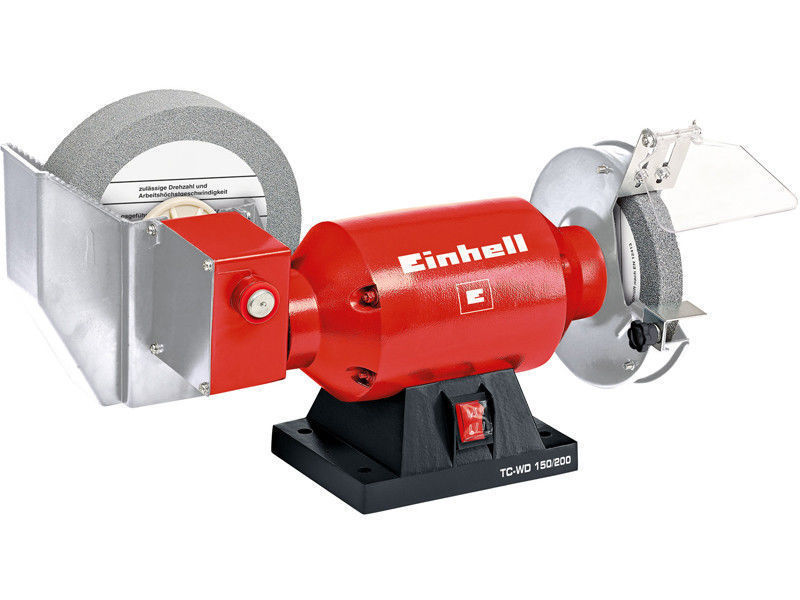
- элементная – получается при обработке сверхтвердого металла, такого как титан, процессы выполняются на низких скоростях;
- слитая – образовывается при высокоскоростной токарной обработке деталей из нетвердой стали, меди, олова, пластмассы;
- надлом – возникает в результате резки металлопластичных деталей;
- ступенчатая стружка получается, в результате обработки металлов средней твердости.
Для разных видов металла подбирается подходящая скорость, так тугоплавкие и сверхтвердые металлы нужно точить на минимальной скорости. Ее рассчитывают перед началом работ и задают в параметры точильного станка, далее скорость поддерживается автоматически.
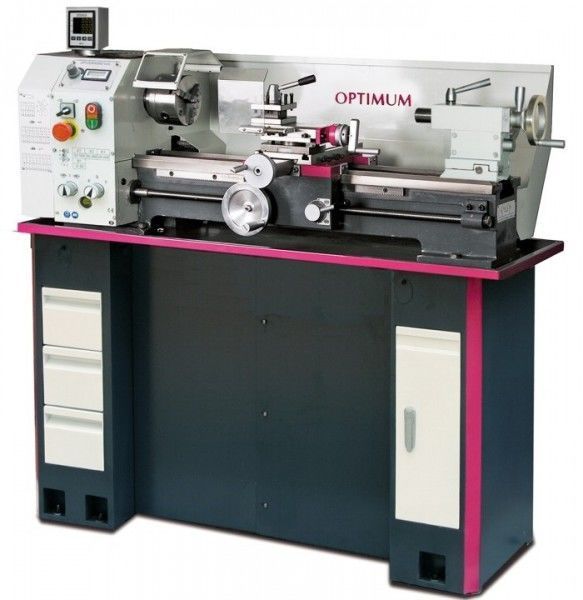
Необходимо понимать, что более точные и чистые работы обеспечиваются на меньшей скорости, а черновые можно осуществлять на максимально допустимой.
Важным моментом являются сплавы металлов, из которых изготовлены резцы. Точило должно быть выполнено из более прочного сплава, чем деталь, которую планируется резать. Наиболее часто для резцов используют титан, вольфрам, тантал.
В зависимости от того какого рода необходима обточка, резцы имеют различные формы и размеры, разнообразие режущих элементов позволит выполнить работы с высокой точностью и меньшим количеством стружки, то есть без значительных отходов.
Резец можно классифицировать по основным видам обработки:
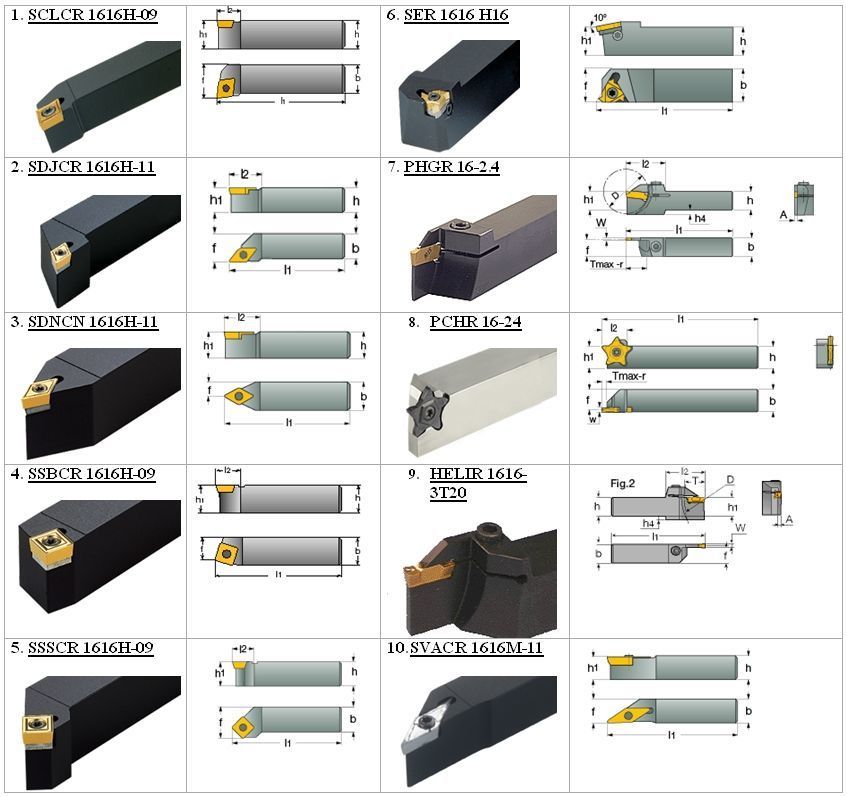
- расточный;
- резьбовый;
- канавочный;
- проходной;
- отрезной;
- подрезной;
- фасонный.
Сам токарный станок может быть механический и автоматизированный с программным пультом управления. Последний дает наибольшую точность и скорость работы, этот вид станков пришел на смену механическим и постепенно вытесняет их с производства.
Все расчеты – скорость, необходимые углы, направления резьбы рассчитываются в программном комплексе, это открывает широкие возможности для производства нестандартных деталей. Если бы для них использовался механический, потребовалось бы значительное время на настройку и не исключен большой процент брака при этом.
Сверление металлических заготовок
Еще одним видом резания металлических деталей является сверление, оно выполняется на соответствующем оборудовании, а сам резак называется сверлом. Суть способа сводится к тому, что сверло или зенкер приводятся в действие механическим способом и вращается вокруг своей оси.
Сверлильный станок. Настройка и другие хитрости
За счёт таких движений инструмент врезается в металлическую деталь, делая отверстие в ней. Сверло приводится в действие ручным приспособлением, механическими и автоматизированными станками. С помощью сверла можно получить отверстия в металлической заготовке разного вида, размера и глубины:
- перовое;
- спиральное;
- центровочное.
Чаще всего встречается спиральный вид сверла, оно состоит из трех частей: рабочей части, шейки и хвостовика. Режущий отрезок имеет две кромки, расположенные под определенным углом по отношению друг к другу, например, для резки чугунной детали необходим угол 118 о.
Сверлильный станок из рулевой рейки
Хвостовик нужен чтобы закрепить сверло в патрон станка или дрель. Он может иметь две формы: цилиндрическую или коническую. На конце хвостовика установлена лапка, которая нужна для выталкивания сверла после использования из гнезда.
Шейка сверла – переходное звено, которое необходимо для обеспечения выхода в процессе шлифования абразивного круга. На шейке ставится маркировка сверла.
Перед началом сверления нужно разметить деталь, центр лучше сделать углубленным с помощью кернера, чтобы в начале работы сверло не слетело с намеченного пункта.
Для сверления металлических деталей могут применяться различные инструменты:

Фрезерование металлических деталей
Обработка металлов резанием с помощью фрезы – это один из самых распространенных способов. Главным режущим элементом в конструкции станка является фреза – круглое колесо, имеющее зубчатые края. Электрический мотор приводит в действие режущий механизм, на большой скорости фреза врезается в металлическую заготовку и снимает слои в нужных местах.
Токарно-фрезерный станок DMG CTX gamma 2000
В итоге получается срез в детали и стружка отработанного материала. Ранее фрезерные станки управлялись только специалистом, из-за больших скоростей и диаметра колеса, получалось много отходов и бракованных деталей. Современные станки управляются программным обеспечением, благодаря чему достигнут высокий уровень точности резки.
Фрезерный станок по металлу корвет 416 Энкор
Фрезы могут быть разных размеров и форм и применяются в зависимости от необходимой величины разреза, вида обрабатываемого металла.
Станки последнего поколения оснащены лазером, который позволяет не только достичь максимальной точности, но и выполнять работы по сложной фигурной резке. Тепловой лазер выжигает кромку в нужных местах, а шлифовальный лазер проходит по нескольку раз по кромке, разрезая металл, такой подход обеспечивает снятие минимального слоя материала заготовки. На выходе получается чистый разрез, без заусениц и сколов, такая деталь не потребует дальнейшей зачистки.
Строгальная резка металла
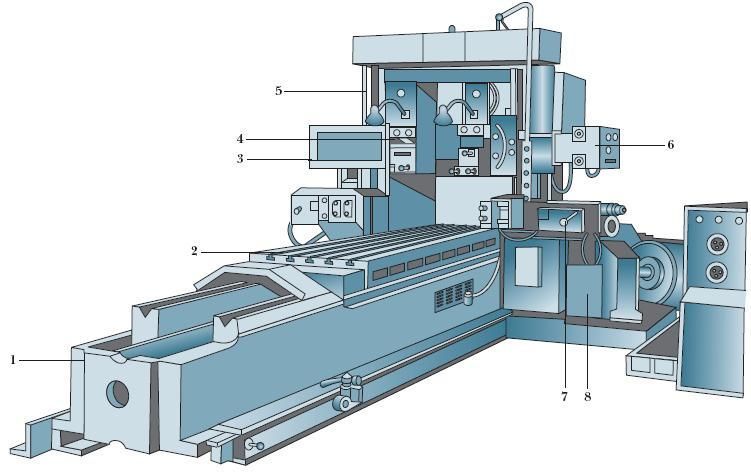
Обработка металла резанием строгальным способом предусматривает снятие верхних слоев поверхности детали, которая обрабатывается. Этот вид обработки предполагает использование специализированных станков:
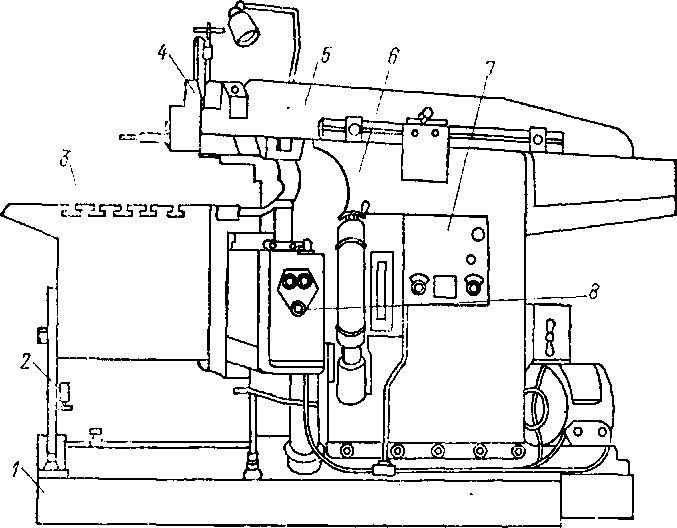
- строгально-долбежных;
- поперечного и продольного сечения;
- кромкострогальных.
Отличаются станки способом движения режущего механизма, производительностью, качеством обработки металла.
Особенностью строгальных установок является использование только прямых строгальных резцов, они устанавливаются на малых вылетах, поскольку не отличаются виброустойчивостью, но достаточно просты в управлении.
Недостаток таких резцов – невозможность получения максимально точных результатов резки. Для устранения этого недостатка некоторые станки имеют возможность для монтажа нескольких резцов.
В работе со строгальными станками важно учитывать, что режущие части достаточно мощные и способны с первого нажатия погрузиться в металл на большую глубину, что может испортить изделие.
Шлифование как способ резки металла
Шлифовальный метод для резки металлических деталей предусматривает использование различных абразивных кругов. Они состоят из мелких зерен, минерального происхождения, которые соединены друг с другом связкой.

Техника резания сводится к следующему процессу: при движении абразивных насадок, острые грани срезают верхние слои металла и оставляют за собой гладкую выемку. Все движения осуществляются на очень большой скорости, иногда она достигает 3000 метров в одну минуту, для сравнения, при токарной обработке максимальная скорость составляет 30 метров.
Из-за высокой скорости и хаотичного расположения зерен получается очень мелкая стружка, которая разлетается во все стороны и на несколько метров. Эту особенность следует учитывать при организации безопасных условий работника.
Шлифовка позволяет добиться точных результатов резки, однако, при этом станок потребляет очень много электроэнергии, в 10 раз больше, чем, например, токарная установка. Еще одной особенностью шлифовки является высокая степень нагрева самой металлической детали, в некоторых случаях до 1000 о. Это необходимо учитывать при обработке мягких металлов, таких как медь, олово, чугун и прочих, от действия шлифовального круга они могут попросту расплавиться.
Видео: Удивительные возможности станков с ЧПУ
В отличие от других видов обработки механическая обработка металла
никак не влияет на внутреннюю структуру металла или сплава, а лишь изменяет ее размеры и конфигурацию. Суть механической обработки – это подгон упрочненной детали под необходимые, заданные по чертежу, размеры. Для проведения механической обработки металла используют режущий инструмент, металлорежущие станки и сварку.
Полученные после такой обработки детали имеют идеальную форму, точные размеры и ровную поверхность, строго соответствующие чертежу. К слову, готовые металлические детали, прошедшие механическую обработку, можно посмотреть на международной выставке «Металлообработка», которая пройдет в ЦВК «Экспоцентр». Там же продемонстрируют и само оборудование, с помощью которого можно проводить механическую обработку, включая новые модернизированные металлорежущие станки.
Как происходит подгон детали под размер?
Механическая обработка металла может проводиться с использованием различного металлорежущего инструмента и в зависимости от него можно выделить несколько видов механического воздействия на деталь:
- Обработка резанием;
- Обработка с пластической деформацией;
- Обработка с использованием метода деформирующего резания;
- Электрообработка.
Обработка металла резанием
Резание чаще всего используют для получения деталей машин. Суть этого метода заключается в том, что после обработки резанием получается новая поверхность металла. Это происходит благодаря деформированию с помощью металлорежущих станков и инструментов поверхностного слоя детали и последующему снятию этих слоев. Этот процесс сопровождается появлением стружки верхнего слоя металла. Стружку, то есть остаточный материал после обработки, называют припуск. Иными словами, это избыточный материал. Его размер должен быть минимальным для снижения трудоемкости и затрат на обработку, но достаточным для получения высококачественной детали с необходимым набором свойств.
В зависимости от инструмента, используемого для механической обработки металла , выделяют несколько видов обработки резанием:
- Точение;
- Фрезерование;
- Сверление;
- Строгание;
- Долбление;
- Шлифование;
- Протягивание.
Существует еще множество вспомогательных видов обработки резанием, они используются в зависимости от внешних показателей самой детали – для обработки внешней и внутренней цилиндрической поверхности или же плоскости.
Обработка металла пластической деформацией и электрофизическая обработка
Пластическая деформация металла используется для изменения формы, конфигурации, размеров и физикомеханических свойств подготовленной детали. Сюда относится ковка, прессование, штамповка, накатка резьбы.
Для электрофизической обработки характерно использование различных явлений электрического тока:
- Электроэрозионная обработка;
- Электрохимическая обработка;
- Электрическая дуговая сварка.
Для достижения максимально продуктивного результата обработки металла на производстве используется широкий диапазон инструментов механической обработки, к наиболее распространенным видам оборудования можно отнести:
- Токарные станки;
- Сверлильно-расточные аппараты;
- Шлифовальные машины;
- Фрезерные и протяжные станки;
- Пресс.
Довольно часто металл после 100-тонного прессования или ковки обрабатывают электрохимическим методом – наносят различные покрытия. Например, металл можно латунировать, никелировать, лужить и прочее.
Метрологические исследования и измерения помогают определить минимальные затраты материала, наименьшие показатели припуска и необходимые для качественной механической обработки металла условия.
В зависимости от выбранного вида обработки механическим путем можно получить массу деталей с различным уровнем шероховатости поверхности и покрытием, размером и отверстиями. Благодаря такому широкому ассортименту инструментов для проведения обработки на производстве получают как мелкие детали (гайки, винты с резьбой, обычные бытовые детали, например дверные ручки), так и более масштабные детали машин – двигателей, строительного оборудования и более сложных механизмов.
Такая на первый взгляд несложная обработка металлов вмещает в себе множество нюансов, упустив один из которых, необходимого результата невозможно будет достичь.
Во многих областях промышленности не обойтись без такого процесса, как механическая обработка металлов. Машины, станки и инструменты постоянно совершенствуются, из года в год операции осуществляются все быстрее. На производственных предприятиях работают станки специализированного и общего назначения. С помощью таких станков легко раскроить заготовки листового, профильного или другого типа. Широко применяются также методы разделения материала: , фрезой, ленточной пилой и прочие.
Технологические процессы механической обработки металлов
Механическая обработка металлов - достаточно сложный процесс, в результате которого получаются детали определенных размеров и заданных форм. Существует два способа механического воздействия на материал. Первый способ выражается в снятии верхнего слоя с рабочей поверхности. При этом глубина может быть разной зависимо от требований, предъявляемых к размерам детали. Во втором способе материал никак не повреждается при первичном воздействии, он может лишь прессоваться, штамповаться, коваться, прокатываться. Как правило, за таким способом воздействия следует этап дальнейшей работы над деталью.
Комплекс технологических операций по приданию определенного размера и формы деталям предусматривает различные виды механической обработки металлов. Основные из них - это работы по точению, фрезерованию, строганию, шлифованию и сверлению. Сейчас все операции проводятся на современных многофункциональных станках. Так, одна и та же машина может выполнять последовательно разные функции. Для этого просто необходимо правильно установить программы и вовремя применять нужные инструменты. Многие названия инструментов говорят об их предназначении: сверло - для сверления, фреза - для фрезерования и так далее.
Все виды механической обработки металлов разнообразны, им свойственные собственные отличия и нюансы. Самым современным способом, отвечающим высокотехнологичным требованиям, является обработка на токарном станке. Они бывают автоматическими, полуавтоматическими и с ЧПУ. Как правило, для обработки фасонных или плоских поверхностей используется фрезерование разных видов: торцевое, концевое или фасонное.
Сейчас множество современных производств предлагают услуги по механической обработке металла. Станков для проведения этих работ существует также немало, но время диктует свои условия, поэтому машины постоянно совершенствуются. Так, примитивные станки уже почти везде заменены на автоматические линии. Динамично развивающиеся предприятия стараются как можно больше расширить производство с помощью высокотехнологического оборудования. Таким образом, с большой долей вероятности можно гарантировать высокое качество выпускаемой продукции и минимальные сроки обработки заказов. Любое производство выигрывает, если принимает за приоритетное направление хорошую выработку качественных изделий, независимо от объема заказа и его сложности.
Оборудование для механической обработки металлов
Как правило, услуги по механической обработке металла выполняются быстро и в полном соответствии со всеми стандартами, когда за работу берется квалифицированный персонал. Кроме этого, каждое перспективное предприятие обеспечивает для работы оптимальные условия: достаточное наличие производственных площадей, необходимое оборудование. Стоит отметить, что для успешного и быстрого выполнения заказа персоналу нужно предоставить станки, сварочное и технологическое оборудование.
Итак, для выполнения работ следует правильно выбрать оборудование механической обработки металлов. Конечно, за основную работу - снятие стружки, отвечает токарное и фрезерное направление. Самое распространенное оборудование в данной сфере - токарные центры с ЧПУ и центры . Современные модели позволяют изготовлять детали, соответствующие самым высоким требованиям относительно геометрических параметров изделия и шероховатости его поверхности. Преимуществами новых моделей станков являются: точность, скорость, улучшенные параметры рабочих зон.
Оборудование механической обработки металлов на настоящий момент представлено в широком ассортименте. Среди многообразия моделей имеются как самые популярные, так и достаточно редкие (относительно часты применения). К примеру, карусельный станок, который способен обработать деталь, имеющую диаметр до девяти метров. Такой станок применяется не часто и не везде. Достаточно востребованы координатно-расточные станки, обеспечивающие качественную расточку под любым углом и станки расточные с поворотными столами. Каждое предприятие, сфера деятельности которого - механическая обработка металла, старается иметь в наличии фрезерные, зубофрезерные, радиально-, горизонтально- и вертикально-сверлильные станки.